3D tisk mění plastikářský průmysl
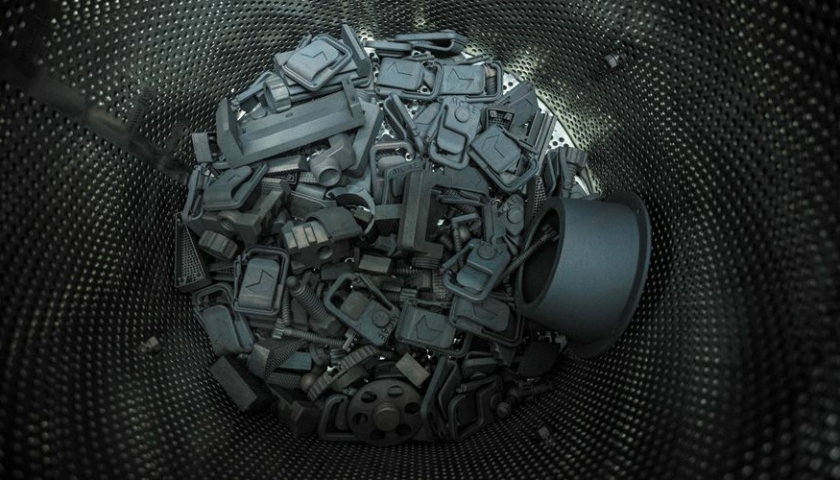
Technologie plastového 3D tisku se neustále zlepšují. Zvyšuje se produktivita, opakovatelnost i přesnost tištěných dílů. Pro zájemce o sériovou výrobu koncových dílů 3D tiskem byl určen seminář firmy MCAE Systems v Kuřimi. Kromě samotného 3D tisku zde byla velká pozornost věnováno také postprocessingu.
Inzerce
Seminář s provokativním názvem „Může 3D tisk nahradit vstřikování plastů?“ nabídl porovnání těchto 2 technologií s důrazem na finanční náklady. Hlavní pozornost byla věnována tiskárně H350 od firmy Stratasys. Bez povrchových úprav a barvení vytištěných dílů je koncový produkt těžko představitelný. MCAE Systems nabízí vhodné technologie od firmy DyeMansion, které na semináři představil Greg Gracki.
Stratasys H350 (foto: Stratasys)
Produktivní aditivní výroba
Poměrně dobře se aditivní výroba zavedla ve výrobě prototypů a přípravků. Řada firem oceňuje tisk náhradních dílů. Výrobou koncových dílů se však zabývá jen minimum firem. V portfoliu společnosti MCAE Systems jsou minimálně 2 technologie aditivní výroby plastových dílů, které jsou vhodné pro sériovou produkci. Hlavním favoritem pro tento typ využití je technologie SAF, kterou využívá tiskárna Stratasys H350. Výhody této tiskárny a podrobné srovnání s konvenčními technologiemi nabídl Jan Drápela.
Obecně platí, že výroba technologií SAF je výhodná pro malé a střední série dílů s rozměry do 10 cm. Konvenční technologie vstřikování do forem osvědčuje svou nenahraditelnost v sériích nad 100 000 kusů a v případě rozměrnějších dílů.
Nyní se podrobněji podívejme na silné stránky aditivní výroby v porovnání se vstřikováním. Především nepotřebujeme pro výrobu žádnou formu, tím odpadnou obrovské fixní náklady na výrobu formy a zároveň se o týdny zkrátí čas, kdy můžeme začít vyrábět. Pro 3D tisk neexistuje minimální série, lze vyrobit i jeden díl. Aditivní výroba také umožňuje produkci složitých dílů, které s pomocí formy vyrobit nelze, nebo si vyžadují komplikovanější, a tedy i dražší, formu. Při výrobě 3D tiskem odpadají přípravné časy, kdy se forma vkládá do stroje a předehřívá se. Firma také nepotřebuje žádnou plochu na skladování momentálně nevyužívaných forem.
Samozřejmě ne každá technologie 3D tisku je pro sériovou výrobu vhodná. Zmíněná tiskárna H350 byla speciálně navržena k minimalizaci nákladů na vyrobený díl. Podstata technologie SAF spočívá v postupném nanášení práškových vrstev na tiskovou podložku, tryskání absorpční kapaliny a následném vytvrzení těchto míst působením infračervené lampy v celé šíři tiskové podložky. Vysoká opakovatelná přesnost tisku je zajištěna kontrolovanou teplotní stabilitou ve stavebním prostoru.
Příklad z firmy Onulis
Výhody tiskárny H350 využila optimálně firma Onulis. Sama vyrábí a prodává 3D tiskárny WRAP, které zpracovávající materiál na bázi pryskyřice. Každý z výrobků obsahuje desítky malých plastových součástí. Po vyzkoušení různých dodavatelů a různých technologií vyrábí Onulis nyní všechny tyto díly na jediné tiskárně H350. Vyráběné díly můžeme rozdělit do tří skupin: jednoduché díly – teoreticky ideální pro konvenční výrobu), složité díly – spíše vhodné pro 3D tisk, velmi složité díly – které jinak než aditivně vůbec není možné vyrobit. U všech těchto skupin došlo přechodem na technologii SAF k finanční úspoře. Dokonce i jednoduché díly jsou nyní o 17 % levnější než od původního dodavatele. Složité díly jsou levnější o celých 37 %. Přínos snadné výroby velice komplexních dílů je zřejmý. Onulis tiskne díly jen pro svojí vlastní potřebu a jeho cílem není maximalizace produkce. V jedné tiskové dávce vyrobí 92 komponentů, což týdně představuje 1 100 dílů, to je dostatečné množství pro výrobu 28 zařízení VRAP každý týden.
Doplněk k CNC obrábění
Jiný příběh nabízí firma Goetz Maschinenbau, která má dlouhou tradici a prioritu v klasickém třískovém obrábění kovů. Někteří zákazníci však od nich chtějí i platové díly, které se dosud vyráběly vždy na vstřikolisu. Goetz Maschinenbau již pár let vlastní jednodušší 3D tiskárny, na nichž tiskne náhradní díly nebo přípravky. Jednatel Philipp Goetz se tedy nezalekl myšlenky na sériovou aditivní výrobu a koupil tiskárnu H350. Ukázala se jako neocenitelný doplněk do portfolia jejich technologií, zvláště v době přetrhaných dodavatelských řetězců. „V současné době vyrábíme hlavně díly o velikosti malíčku, tak malých dílů můžeme do tiskové komory vyskládat přibližně 1 000. Znamená to, že během 24 hodin jsme schopni vyrobit celou zakázku. V několika týdnech dokážeme díky 3D tisku dodat zákazníkům desítky tisíc dílů, což jsou čísla, která bychom vstřikováním v tak krátkém čase nikdy nebyli schopni realizovat – a už vůbec ne za takovou cenu,“ vysvětluje Philipp Goetz.
Od výtisku po finální produkt
Díl z 3D tiskárny se blíží svým vzhledem finálnímu výrobku, ale ve skutečnosti ho od něj dělí ještě minimálně 3 kroky velmi podstatných úprav. Jak k postprocessingu přistupuje firma DyeMansion vysvětlil ve svém příspěvku Greg Gracki. Sama společnost DyeMansion se pyšní tím, že jako jediná na světě nabízí stroje na všechny 3 kroky úspěšného zpracování výtisku, a totiž čištění, úpravu povrchu a barvení. Další výhodou jejich strojů je dosledovatelnost každého výrobku dle principů Průmyslu 4.0.
Prvním krokem je důkladné vyčištění dílů od zbytků prášku. To se děje v pračce, která je navržena tak, aby vyčištění bylo opravdu důkladné a spolehlivé. Pokud jste někdy ručně čistili díl z tiskárny, víte, jak obtížné je zbavit zbytků prášku opravdu všechna zákoutí. Čištění trvá zhruba 10 až 15 minut, takže pokud tisknete kontinuálně i na více tiskárnách, plynule můžete posouvat díly do čisticího procesu. Všechny operace, o kterých Greg hovořil, jsou vhodné pro většinu typů výtisků z PA20 a podobných materiálů, takže vedle tiskáren Stratasys využijí stroje firmy DyeMansion i majitelé tiskáren HP, EOS a dalších.
Druhým krokem je ohlazení povrchu na stroji Powershot S v míře, kterou si sami zvolíte. Snížení mikrovýstupků na povrchu dílů má za následek zhutnění povrchové vrstvy, a tedy i zpevnění celého výrobku, a také třeba snížení jeho nasákavosti a zvýšení odolnosti proti poškrábání.
Úpravou, která dílu skutečně vdechne život, je barvení. Probíhá na stroji označeném MD60. V tomto kroku se nenanáší žádná nová vrstva, ale díly se penetrují barvou do hloubky 200 mikronů. Výběr barev je prakticky neomezený. Pokud si zákazník přeje specifický odstín barvy, potřebuje firma 3 týdny na to, aby přesnou barvu v požadované kvalitě připravila. Barvy mají certifikát pro využití v potravinářství a jsou odolné proti teplu, světlu i UV záření. V automobilovém průmyslu již existují zkušenosti s používáním takto barvených dílů v těsném sousedství s díly lakovanými a vizuálně mezi nimi není rozdíl.
Další článek: Seminář Technologické trendy využití 3D tisku v průmyslu