3D tisk v malosériové výrobě
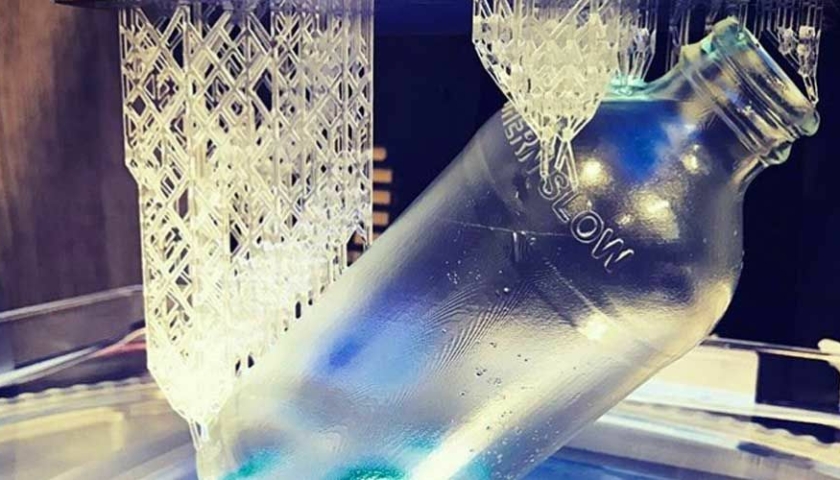
Mnohé z těch, kdo se dnes seriózně věnují profesionálnímu 3D tisku, k těmto technologiím přivedla náhoda, když hledali řešení konkrétního konstrukčního problému pro své vlastní potřeby. U firmy Cotu to nebylo jinak.
Inzerce
Showroom Cotu v pražské Libni napovídá, že pokud jde o 3D tisk, mají s ním zdejší lidé opravdu hodně zkušeností. Začali s ním před několika lety, když se dnešní provozní ředitel Daniel Jankovič a jeho společník, produktový designér Daniel Zach, snažili vyvinout pozemní plachetnici s karbonovým trupem. „Dělali jsme si vlastní design, při kterém jsme narazili na problém s výrobou forem. Standardní řešení – frézování – se ukázalo jako nákladné a navíc znamenalo změnit konstrukci plachetnice, což jsme nechtěli dopustit,“ vzpomíná Daniel Jankovič.
Rozhodli se proto zkusit aditivní výrobu, se kterou dosud neměli zkušenosti. Oslovili dodavatele tiskových služeb a v mezičase navštívili výstavu 3Dexpo. Odtud pro ně vyplynulo překvapivé zjištění – že je bude vytištění požadovaných dílů na zakázku stát zhruba stejně tolik, jako pořízení celé vlastní 3D tiskárny, kterou si na výstavě v Letňanech tenkrát vyhlédli. Rozhodnutí bylo jednoznačné – firma si pořídila svoji první tiskárnu značky Zortrax, která nabízela spolehlivý tisk z požadovaného materiálu ABS, což v dané cenové relaci nebylo standardem (většina výrobců se tou dobou soustředila na tisk z jednoduššího materiálu PLA). Kvůli menší tiskové ploše Zortraxu musela být plachetnice tištěna po částech. Celkově vzniklo 46 segmentů, z nichž bylo následně sestaveno 16 master modelů. Aby byly zachovány přesné tvary a ostré linie, musely být výtisky ručně obroušeny. Na některé části pak bylo aplikováno v tenké vrstvě ještě tmelení a celé výtisky pak byly finálně opatřeny lakem. Tímto postupem bylo docíleno finální podoby požadované formy. „Po jednom měsíci práce tří lidí jsme v rukou drželi náš první laminátový odlitek velmi složitého designu.
Mohu říci, že mezi povrchem výrobku právě vyndaného ze 3D tiskárny a jeho finální podobou je dlouhá cesta, které je potřeba věnovat péči a píli. Díky výše popsané zkušenosti jsme si uvědomili, že takováto ucelená služba na českém trhu chybí,“ konstatuje Jankovič. Tak se zrodil nápad založit firmu, která na bázi 3D výtisků – považovaných za polotovar – nabízí ucelený a domyšlený produkt s ohledem na malosériovou výrobu.
Spousta pečlivé ruční práce
V Cotu vám potvrdí, že 3D tisk vhodně doplňuje jiné technologie, nehodí se pro všechno a finální produkt se neobejde bez velkého množství ruční práce. Zákazník očekává funkční a odolný produkt s pěkným povrchem. „Každý projekt je jiný. Naučili jsme se relevantně odhadovat náklady a čas potřebný pro realizaci. Nejdůležitější bylo ale najít vhodné lidi se smyslem pro detail, schopné vnímat nové materiály, pracovat s moderními technologiemi a nalézat lepší postupy povrchového opracování. Uvědomili jsme si, že propojením technologií lehce docílíme i malosériové výroby.“ Jako servisní kancelář s vlastním širokým know-how v aditivní výrobě Cotu pomáhá ostatním firmám vstoupit na trh s první sérií vlastního výrobku téměř na počkání. „Díly, které vyrábíme strunovou tiskárnou Zortrax, lze použít jako nepohledové, například uvnitř zařízení. Lze je ale posílit kovovou vložkou, orientací dílu nebo vhodným výběrem odolného materiálu, a proto jsou využitelné i pro náročné aplikace, třeba jako díly výrobní linky.“
Matné pohledové a funkční díly pak v Cotu vyrábí vysoce detailními metodami DLP a SLA na 3D tiskárnách Asiga z produkčních fotopolymerů nové generace, které v průběhu let nezkřehnou. Tyto firma sama připravuje a chystá se je prodávat pod vlastní značkou zaměřenou na ekologické materiály.
Výrobek na míru – na počkání
Typickým zákazníkem Cotu je firma, která řeší zpracování výrobku ještě v jeho prototypové fázi. Kupříkladu může jít o zákazníka z oblasti internetu věcí, který již disponuje prvotním konstrukčním návrhem, jenž je však potřeba dopracovat z hlediska designu a dovést do malosériové výroby. „Většinou je před nás předložena hranatá krabička, vytištěná ještě na strunové 3D tiskárně a v ní fungující elektronika. U nás během několika hodin navrhneme designový koncept obsahující několik variant, jak by produkt mohl vypadat. Z prvků, které se zákazníkovi líbí, vytvoříme finální návrh, ten vytiskneme jako maketu a po schválení zapojíme do procesu konstruktéra. Různé funkční nebo mechanické prvky, zácvaky a uchycení vymýšlíme v týmu i s ohledem na další rozvoj a samotné sestavení. Finální 3D model je pak vytištěn a pečlivě povrchově opracován. Klademe důraz na ostré hrany, rovné plochy bez propadů, rovné spoje mezi díly a na strukturu povrchu.
Takto připravený model zalijeme do silikonu, vyhotovíme několik forem, z kterých díly odléváme ručně ve vakuu v malých sériích o počtu deseti až tisíce kusů. Odlitky se musí temperovat, ručně začistit a sestavit. Každému dílu je tak věnována samostatná péče. Výrobek je pak na trhu během měsíce, přičemž se náklady udrží v řádech desítek tisíc korun. Dalším benefitem je možnost již v průběhu výroby produkt dále rychle vylepšovat,“ popisuje Daniel Jankovič výrobní proces, který je nedílně spojen s procesem vývojovým.
Dosavadní zákaznická produkce zahrnuje výrobky nejrůznějších tvarů, velikostí i barev. Od titěrných věcí, jako kamerové krytky, prototypů hodinek, vytavitelných šperkařských modelů nebo koncovek na naslouchátka, přes zubní náhrady, krabičky pro spotřební elektroniku, designové brýle pro virtuální realitu, díly pro letectví a armádu, odlehčené řadicí páky pro veřejnou dopravu, prototypy světlometů, až po marketingové produkty, ať už jde o makety lahví pro výrobce colových nápojů, individualizované stylusy pro chytré telefony nebo rozličné reklamní postavičky… V Cotu takto realizují během roku více než 250 různých projektů a každý další představuje novou výzvu.
Další článek: Ambiciózní projekt na automatizaci výroby filtrů se zrodil v Acam Solution v Brně