Digitální transformace v TAJMAC-ZPS: dlouhodobá usilovná práce přináší hmatatelné výsledky
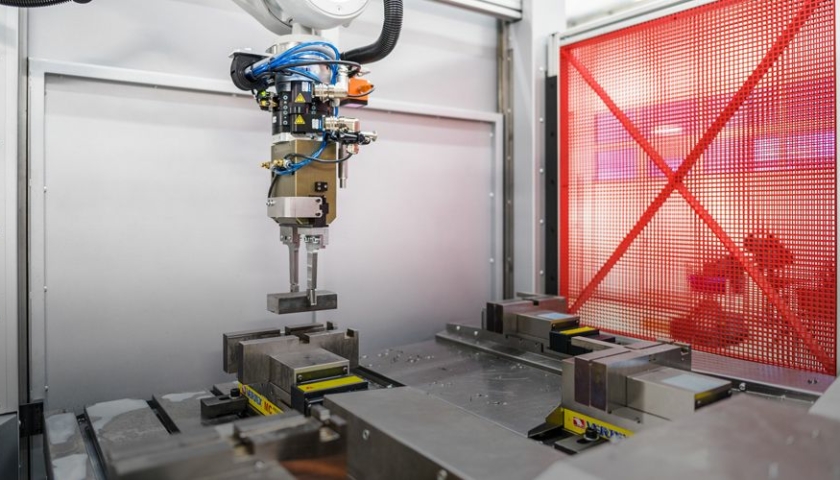
Základní otázka zní: Je v oboru vývoje obráběcích strojů kam pokračovat? Vždyť produktivita strojů je už nyní tak vysoká a jejich pracovní schopnosti jsou na pokraji technických a fyzikálních možností. Přesto je odpovědí jasné ANO.
Inzerce
Vize dalšího rozvoje popisuje koncept Průmysl 4.0. Směřuje k chytrým továrnám, jež se budou skládat z inteligentních, navzájem komunikujících strojů. Konstrukce, výkon a provedení stroje jsou nesmírně důležité a jsou základem všeho, ale o prodeji stroje budou v budoucnu jednoznačně rozhodovat především jeho přidané vlastnosti. Zlínská firma TAJMAC-ZPS, má ve vývoji, výrobě a prodeji obráběcích strojů dlouholetou tradici. Je tedy zcela logické, že se vydala cestou digitální transformace.
Průlom díky PLM systému
Cesta digitální transformace započala již v roce 1993, kdy byl zahájen přechod konstrukčních prací z prken ke 3D CAD systému, jímž je v současnosti Creo (dříve Pro/Engineer). Konstrukční práce byly podporovány FEM výpočetními metodami. Průlomovým mezníkem vytvoření digitálního vlákna továrny byla před několika lety implementace PLM systému Windchill, který sjednotil pracovní prostředí konstrukcí a napojil se na ostatní podnikové IT systémy. Tento krok umožnil zapojit všechny oddělení předvýrobních etap do jednotné databáze nakupovaných a vyráběných komponent. Odpadla řada ručních a zdlouhavých prací. Schvalování výkresové dokumentace je prováděno v elektronické podobě. Digitální výkresy umožňují automatické vydávání a tisk výkresové dokumentace pro výrobu. V celopodnikové databázi jsou spravovány více než 3 miliony položek od 3D modelů, výkresů, sestav, návodů ke stroji, nakupovaných komponent, výpočtových zpráv, zpráv zkušebny, přejímacích protokolů až po zálohy PLC ke stroji. Vše dostupné on-line ze kteréhokoli místa na světě s připojením na internet.
Roku 2017 byla definována jednotná strategie společnosti ve vztahu ke konceptu Průmyslu 4.0, postavená na 4 základních pilířích: komunikace stroje s okolím, digitalizace výroby, digitální dvojče a automatizace.
Komunikace jako základ
Komunikace je základ úspěchu a klíčový fenomén, bez něhož to prostě nejde. Komunikovat znamená žít, řídit a vést. Vývojoví pracovníci TAJMAC-ZPS připravili komunikační rozhraní stroje, založené na bázi průmyslového standardu OPC UA. Přes toto komunikační rozhraní jsou dostupné veškeré informace o provozu stroje on-line. Běžně dostupné jsou informace o stavu stroje, chybové hlášky, nastavení overridů, teploty motorů, proudové zatížení pohonů a spousta dalších užitečných informací, se kterými může uživatel dále pracovat. Stroj s touto funkcionalitou je snadno integrovatelný do IT struktury podniku a je nezávislý na řídicím systému stroje. Datová struktura je jednotná pro všechny stroje produkce TAJMAC-ZPS. Komunikační modul je nabízen jako opce ke strojům s názvem Industry 4.0. Komunikace se strojem je obousměrná s vysokým stupněm zabezpečení a ochrany dat. V budoucnu bude pro zákazníky dostupný datový standard UMATI, jenž sjednocuje datovou strukturu bez ohledu na dodavatele stroje a umožňuje tak snadnou integraci jakéhokoli stroje do podnikového IT prostředí.
Digitalizace výroby v praxi
Dlouhodobé motto firmy zní: Dříve, než uvedeš něco na trh, odzkoušej si to ve vlastní výrobě. Nejinak tomu bylo i s opcí Průmysl 4.0. Tato opce se stala základním stavebním kamenem a je postupně nasazována na stroje jak z produkce vlastní, tak i na stroje jiných dodavatelů, které firma používá. Pro samotný monitoring výrobních prostředků byla vyvinuta vlastní aplikace s názvem RECON. Aplikace on-line poskytuje základní informace o stavu strojů, probíhající výrobě i pracovnících, kteří jsou do výroby zapojeni. Nad systémem běží reporting, který pomáhá analýze plnění výkonových norem, analýze prostojů, vyhodnocuje náklady na výrobní operaci. Všechny informace o výrobě jsou předávány nadřazenému ERP systému, který je používán pro operativní plánování výroby. Součástí systému je rovněž propracovaný systém hlášení a evidence poruch stroje. Každý pracovník má k dispozici datový terminál, jehož pomocí se přihlašuje ke stroji, volí si operaci z plánované fronty práce, eviduje neproduktivní časy, komunikuje s technology nebo se strojní údržbou. Datový terminál rovněž slouží jako zdroj informací k výrobní dávce nebo k nahlášení poruchy stroje.
Software je nadále vylepšován na základně informací z výroby a má dostatečný potenciál k případnému nasazení i u jiných společností.
Digitální dvojče
Digitální dvojče je dnes často skloňovaný pojem. Jedná se o mechatronický duplikát stroje, s jehož pomocí lze simulovat požadovaný proces. Stavbou takových dvojčat se zabývali již technici v ZPS na počátku 90. let minulého století. Na stavbě současných dvojčat spolupracuje TAJMAC-ZPS s dodavateli řídicích systémů a výzkumnými organizacemi, především s RCMT ČVUT Praha. Správně postavené digitální dvojče umožní testovat vlastnosti stroje již ve fázi ranného návrhu. Vývoj probíhá paralelně s konstrukcí stroje a dokáže až o 30 % zkrátit čas potřebný pro uvedení výrobku na trh. Velkou výzvou jsou v současnosti aplikace cloudových řešení s využitím algoritmů strojového učení a umělé inteligence.
Bude automatizace pro každého?
Strojírenská výroba se dnes automatizuje neuvěřitelným tempem. Zvyšování produktivity se hledá především v automatizaci výrobních operací. Robotické buňky již nejsou výsadou velkých podniků s hromadnou výrobou. Dobu covidové pandemie využil TAJMAC-ZPS k intenzivnímu vývoji automatizované robotické buňky s akceptací pravidel definovaných v konceptu Průmyslu 4.0. Motivací k postavení takovéto buňky bylo primárně lepší časové využití CNC stroje a navýšení výrobní kapacity bez navýšení nákladů na jeho obsluhu. Požadavek pracovníků výroby byl, aby zavedení nové práce do robotické buňky bylo jednoduché a intuitivní, bez nutné znalosti programování klíčových prvků buňky, jako je robot nebo kamerový systém. Takto zavedená výroba součásti musí být snadno a rychle opakovatelná bez dodatečných úprav. Operátor buňky by měl být k dispozici pouze na ranní směnu pro učení nových dílů, na 2. a 3. směnu by měla pracovat buňka bezobslužně. Mimořádně musí být buňka připravena i na sobotní a nedělní bezobslužný provoz.
Výrobní buňka 4.0
Ve spolupráci s výzkumnou organizací Intemac ve Zlíně postavili automatizovanou výrobní buňku, naplňující myšlenky Průmyslu 4.0. Firma TAJMAC-ZPS je schopna předvést a nabídnout řešení pro opakovanou kusovou a malosériovou produkci dílů s hmotností do 7 kg. Výrobní buňka je již nasazena ve vlastní výrobě. Skládá se z inovovaného vertikálního centra MCFV 1260i, které je doplněno automatickým výměníkem palet. Každá paleta má přívod energie. Napájení palet energií je možné jak v paletovém prostoru, tak i v pracovním prostoru stroje. O vstup polotovarů a výstup hotových výrobků se stará pásový dopravník, jehož kapacita je navržena tak, aby byla dostatečná pro bezobslužný provoz alespoň po dobu 60 hodin. Pro manipulaci s obrobky je používán robot s nosností až 40 kg. Dle velikosti úchopu buňka automaticky volí jednu ze dvou velikostí chapadel. Upínání obrobků obstarávají 2 samostředicí svěráky, které mají volitelnou sílu upínání a řízený rozsah rozevření čelistí. O polotovary na vstupním pásu dopravníku se stará 2D kamerový systém s unikátní technologií rozpoznávání tvarů a rozměrů metodou umělé inteligence.
O řízení celé buňky se stará integrační platforma dodaná společností B&R Automation. Výrobní buňka 4.0 je skutečně unikátní, především otevřeností pro připojování nových i současných technologií. Všechny komponenty buňky mají svůj vlastní řídicí systém. Běžně by spolu nemohly komunikovat, ale prostřednictvím integrační platformy ve Výrobní buňce 4.0 to je možné. Navíc jednotné ovládací rozhraní umožňuje spravovat všechna zařízení z jednoho panelu. Právě komunikací mezi zařízeními v této jednotce, ale také konektivitou, demonstruje výrobní buňka některé z podstatných principů širokého konceptu Průmyslu 4.0. Výrobní buňka spojuje zařízení, která jsou běžně dostupná na trhu, ale pracuje s nimi inovativním způsobem.
Celá buňka je osazena řadou bezpečnostních prvků, které slouží pro zajištění bezproblémového a bezpečného chodu všech zařízení. Kontroluje, zda jsou k dispozici správné polotovary, zda je obrobek náležitě upnutý, zda má buňka dostatečný počet nástrojů pro výrobní dávku, je prováděna inprocesní kontrola nástrojů a vyráběných dílů. Buňka je pomocí rozhraní OPC UA napojena jak na celopodnikový monitoring výrobních zařízení, tak i na ERP systém, který sestavuje frontu práce pro výrobu. Po dokončení vyráběných součástí jsou informace přenášeny zpět do ERP systému, který může plánovat výrobu tak, aby bylo ekonomicky vyrobeno jen to, co bude následně spotřebováno. Není tedy nutné plánovat velké dávky, které pak z důvodu provedených změn na součásti leží skladem s rizikem následné nepoužitelnosti.
Dosavadní výsledky a zkušenosti ukazují, že digitalizace je správnou myšlenkou. Je však nutno si stále připomínat, že digitalizace není cíl. Je to jen cesta, jak v budoucnu dosáhnout lepších výsledků s menším úsilím.
Další článek: „Už je to tady“ – Mezinárodní strojírenský veletrh v Brně