Saňové zkoušky aut se podobají crash testům, ale vyjdou mnohem levněji
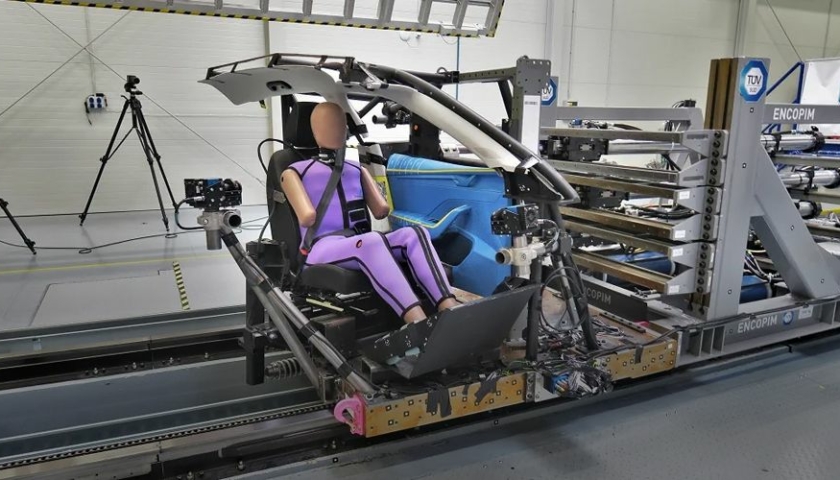
Jak testovat bezpečnost vozidel a nezničit při každém testu jeden prototyp automobilu? Odpovědí jsou saňové zkoušky, které jsou nedestruktivní a přitom otestují všecchny bezpečnostní prvky stejně dobře.
Inzerce
Saňové zkoušky nejsou obecně až tak známým pojmem jako jsou například crash testy. U nich se hned každému vybaví zkouška, kde automobil se zkušebními figurínami nabourá. Ale co si představit pod pojmem saňová zkouška? V principu jde o zjednodušené crash testy, pomocí nichž se zkouší různé kombinace zádržných systémů pro zvýšení bezpečnosti vozů. Pojďme se podívat na nejmodernější technologie, které se při saňových zkouškách používají.
Saňová zkouška zahrnuje mnoho způsobů testování. Jedná se o nedestruktivní formu zkoušek, kterými lze simulovat crash test. Saňové zkoušky se provádí pomocí katapultu, jenž dokáže redukovanou část automobilu se zkušebními figurínami po kolejích zrychlit až na několik desítek násobků zatížení G. Princip těchto testů vychází z jednoduché fyzikální podstaty o zachování energie. To znamená, že při crash testu se nejčastěji zrychlí vozidlo na předepsanou rychlost a poté se střetne s pevným předmětem. Následkem této srážky se posádka setrvačností pohybuje směrem, kterým jelo vozidlo před srážkou. Posádku poté zachytí prvky pasivní bezpečnosti, jakými jsou například airbagy nebo pásy. Principů, jak tento crash test napodobit, je několik. Saňové zkoušky se dělí dle svého principu do dvou hlavních kategorií. Akcelerační a decelerační. Nejmodernější saňové zkušebny využívají především z důvodu lepší shody s crash testy akcelerační přístup, což znamená, že na rozdíl od crash testu vše probíhá reverzně. Zkouška začíná z nulové rychlosti a zkoumané vozidlo se pomocí dynamického katapultu pozpátku zrychlí. Při tomto manévru na posádku působí přetížení ekvivalentní crash testu. Díky tomu lze zkoušet funkci zádržných systémů bez destrukce karoserie a zároveň lze zkoumat jejich dopady na poranění posádky. Potenciál saňových zkoušek spočívá především v laboratorním prostředí, kde jsou vstupní podmínky vždy stejné. Navíc jedna saňová zkouška stojí zlomek toho, co výroba a destrukce celého prototypového automobilu.
Boční nárazy
Dle předpisů musí každý nový automobil splnit dva hlavní požadavky na boční náraz. Náraz na kůl simulující nehodu vozidla, které se dostane do smyku a stranou řidiče narazí do stromu. A na náraz bariéry simulující nehodu, kde jiné vozidlo narazí do stojícího na řidičově straně. Kromě předepsané legislativy se oba tyto typy zkoušek objevují i ve spotřebitelských testech NCAP. Právě spotřebitelské testy NCAP jsou největší motivací automobilek vyrábět vozidla stále bezpečnější a plnit přísná kritéria pro dosažení maximálního počtu hvězdiček. Požadavky organizace NCAP se pravidelně pozměňují z důvodu zvyšování bezpečnosti posádky. Proto se mezi boční testy od roku 2020 dostala také ochrana řidiče při nárazech ze spolujezdcovy strany, takzvaný „far side“ test. Společně s touto zkouškou se zkoumá i interakce mezi hlavami řidiče a spolujezdce při standardním bočním nárazu. Právě sekundární kontakt hlav obou pasažérů může zapříčinit vážná poranění, a proto je v posledních letech vyvíjen nový typ airbagu, takzvaný centrální airbag. Tento airbag se rozbaluje mezi posádku z vnitřní strany opěradla, nebo ze stropního obložení a zabraňuje kontaktu mezi pasažéry.
Dynamické prostředí
Problémem bočních nárazů je velmi nestabilní dynamické prostředí. V obou konfiguracích nárazů (kůl/bariéra) se při crash testu struktura vozu velmi znatelně deformuje. U měkkých automobilů jde o intruzi do interiéru klidně až o 400 mm. Tato deformace se navíc odehrává v rychlém časovém sledu. Deformace a celý náraz trvá zhruba 0,2 vteřiny, přičemž špičky biomechanického zatížení na zkušební figuríně jsou kolem 0,06 vteřiny od nárazu. Za tento čas musí automobil provést velmi mnoho úkonů. Musí identifikovat, že jde o srážku, vyhodnotit, o jaký náraz jde (čelní, boční, zadní, rollover), a spustit prvky pasivní bezpečnosti. U bočních nárazů se typicky jedná o předepínač pásu, boční, hlavový a centrální airbag. Tyto airbagy se běžně rozbalí do 0,03 vteřiny od začátku nárazu a poté do nich začne nalehávat torzo figuríny. Právě tento velmi rychlý děj společně se značnou intruzí do interiéru dělá z bočních nárazů jednu z nejsložitějších saňových zkoušek. Pro její provedení se používají speciální zařízení, kterých je v Evropě jen velmi málo. Unikátní zařízení, jediné svého typu s označením ALIS (Active Lateral Intrusion Simulation) od španělské firmy ENCOPIM využívá firma TÜV SÜD Czech v Mladé Boleslavi.
Technologie katapultu
Zařízení pro testování bočních nárazů je součástí moderní zkušebny DYCOT, která byla do provozu poprvé uvedena v roce 2016. Budování této laboratoře zabralo necelé tři roky a obnášelo investici přes 100 milionů korun. Výsledkem je prostor, jehož srdcem je obří katapult firmy INSTRON, který dokáže urychlit jednu tunu nákladu až na 90 násobků gravitačního zrychlení. K dosažení takového přetížení je potřeba síla zhruba 250 tun. Katapult pracuje na hydraulicko-pneumatickém principu s pracovním tlakem 300 barů v šesti zásobnících. Na kolejích před katapultem se pro boční nárazy nachází unikátní zařízení ALIS, které při bočních nárazech generuje intruzi do interiéru a vytváří společně s katapultem korektní zatížení zkušební figuríny. ALIS má tři pneumatické písty, které dohromady generují sílu až 24 tun. Systém má velmi složitou logiku ovládání, jelikož v jeden moment musí perfektně synchronizovat všechny tři písty a hlavní pulz katapultu. Řízení pístů ALIS probíhá pomocí hydraulických brzd, jejichž princip je podobný brzdám v automobilu. Zjednodušeně si to lze představit tak, jako byste sešlápli pedál brzdy několikrát během 0,06 vteřiny. Řízení této brzdy probíhá zpětnovazebně, což znamená, že systém si sám dokáže neočekávané vnější síly kompenzovat pro dokonalou reprezentaci zadaného výsuvu pístu.
Saňové zkoušky
Boční saňová zkouška, zejména v konfiguraci pro náraz na kůl, je vždy velkou výzvou pro celý vývojový tým. Přípravy těchto zkoušek trvají z důvodů obrovské náročnosti na přesnost i několik měsíců. Odchylka byť jen 10 milimetrů oproti crash testu může znamenat odlišné chování bočního airbagu, a tedy i špatnou biomechanickou odezvu figuríny. Přesnost je tak základním předpokladem úspěchu. Veškeré přípravy začínají ještě před tím, než reálné vozidlo projde prvním crash testem. Vstupem do saňové zkoušky je virtuální FE simulace (Finite-element method) celého vozidla. Tento model se zredukuje pouze na součásti potřebné k saňové zkoušce – tedy na sedačku, pásy, díly interiéru a airbagy. Redukovaný model se poté detailně zkoumá, kde a jakým způsobem dochází k intruzi do interiéru v návaznosti na kontakt s figurínou. S využitím velmi zkušeného vývojového týmu se poté navrhne intruzní mechanismus, který díky systému několika pohyblivých dílů přesně reprezentuje deformaci interiéru. Intruzní mechanismus funguje při reálné zkoušce jako nosič interiérových dílů a jako náhrada karoserie, jež se však po každém testu nemusí měnit. Jakmile je nastavena deformace interiéru, je na řadě synchronizace a ladění řídicích pulzů jednotlivých pístů tak, aby biomechanická odezva figuríny byla ekvivalentní crash testu. Biomechanickou odezvou je především myšleno zatížení hrudníku a ramene, společně se zrychlením hlavy. Tato část zabere většinou nejvíce času, kdy se vytváří matice zhruba dvou set simulací a postupně se iteruje chování figuríny. Dle složitosti modelu zabere jedna simulace 4-10 hodin výpočetního času.
V momentě, kdy je virtuální část hotova, přicházejí data z prvního crash testu vozu. Po jejich analýze se vytváří iterační smyčka zpřesnění virtuálních simulací, aby co nejvíce odpovídaly realitě. Samotná saňová zkouška je poté už jen špičkou ledovce fáze dlouhých příprav. Naladění zařízení ALIS trvá přibližně pět zkušebních výstřelů, kde se porovnávají rychlosti na jednotlivých pístech, případně rychlosti interiérových dílů s crash testem. Základem zkoušky je pohyb dílů interiéru. Ty musí být v určitém čase na přesně daném místě, tak aby se správně rozbalil airbag. O jejich pohyb se starají písty zařízení ALIS a jakmile je korektně rozbalený airbag, přejímá hlavní činnost katapult, který figuríně uděluje správný pohyb. Když se vše podaří dobře synchronizovat, biomechanická odezva na figuríně dává velmi shodné hodnoty s crash testem. Po naladění celého systému se vyzkouší opakovatelnost, tedy zkouška, zda-li dva testy podávají stejné výsledky, a poté se přechází k té nejdůležitější části a tou je vývoj. Testují se odlišné typy airbagů nebo různé konfigurace zádržných systémů. Výsledným kritériem vývoje je biomechanické zatížení figuríny. Především se sleduje závažnost poranění posádky.
Projekty
První boční saňové zkoušky v TÜV SÜD Czech začaly v roce 2017 a za tu dobu se na zařízení ALIS vystřídalo mnoho renomovaných automobilek. ALIS má za sebou kolem stovky testů, při kterých se odhalilo mnoho výrobních nedostatků airbagů, nebo se podařilo najít vhodnější nastavení pro snížení poranění posádky. Největší výhodou zařízení ALIS je bezpochyby jeho variabilita. Díky mnohaletým zkušenostem expertů v oblasti bočních nárazů může vývojový tým přizpůsobit zkoušku přesně zadaným požadavkům. Lze tedy předem navrhnout systém tak, aby reprezentoval například zatížení na rameni nebo se soustředil na korektní chování airbagu. V současnosti je systém schopný zkoušet dohromady přední i zadní figurínu v případě nárazů na bariéru a aktuálně se vývojáři zabývají zkouškami occupant to occupant, tedy interakcí mezi řidičem a spolujezdcem, která by do budoucna měla být řešitelná v rámci jedné saňové zkoušky.
Technologie na prvním místě
Pro splnění předpisů a naplnění požadavků na reálnou bezpečnost vozů je ale klíčové chápat potřebu saňových zkoušek jako jeden z pilířů komplexního systému vývoje. Ten začíná u virtuálních simulací určujících vývojový směr, saňové zkoušky tento směr potvrdí v reálném prostředí a na závěr se vše ověří při crash testu. Tento proces se velmi často cyklicky opakuje a jakmile by jeden z těchto pilířů vývoje vypadl, znamenalo by to větší rizika při reálných nehodách a pravděpodobně také nákladnější variantu vývoje pro automobilky. TÜV SÜD Czech je v tomto vývojovém cyklu hrdým partnerem automobilek a díky dobrým výsledkům pomáhá ALIS zlevnit a zrychlit vývoj vozů.