Automatický vozík Toyota Autopilot ukládá materiál až do výšky 4 metry
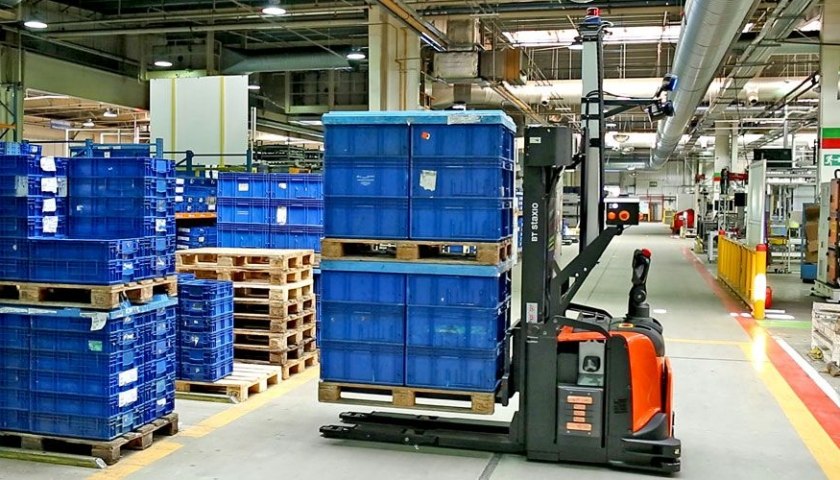
Společnost Faurecia Components Písek, s.r.o., významný výrobce pro automotive sektor, realizuje společně s Toyotou unikátní řešení automatického převozu nákladu a jeho stohování pomocí vozíku Autopilot SAE160 založeného na šasi řady ručně vedených zakladačů BT Staxio.
Inzerce
Faurecia Components nasazuje automatický stacker s unikátním řešením navigace od Toyoty
Projekt se po více než dvouleté technické přípravě, ladění a důkladného testování všech detailů posunul do fáze, kdy oba aktéry čeká finální předání projektu uživateli do reálného provozu.
V ČR postavila skupina Faurecia již 7 výrobních závodů. V mladším z obou píseckých závodů společnosti se vyrábějí rámy sedaček pro významné evropské automobilky. Továrna Faurecia Components byla otevřena v roce 2011 a ve třísměnném provozu zaměstnává 550 zaměstnanců. Vozík Autopilot SAE160 je nasazen v logistické sekci výrobní haly a vysvětlení jeho činnosti se ujal Václav Mareš, Improvement coordinator v logistice Faurecia Components:
„K zásobování výrobních linek používáme systém vláčků, které rozvážejí komponenty přímo k výrobním linkám a k jednotlivým výrobním stanovištím v malých KLT boxech různých typů. Když jsou vyprázdněny, operátoři je pečlivě vyskládají na paletu, zakrytují víkem a po dvou na sobě uloží do zóny, ze které si je později odebere automat, aby je odvezl do centrálního skladu, odkud se vracejí dodavatelům. Dosud tuto činnost vykonával jeden operátor s vysokozdvižným vozíkem. Ze skladu se automat vrací zpět pro další náklad. Zatím se vrací prázdný, ale to chceme v budoucnu změnit a plně ho vytížit i na zpáteční cestě."
Zavření závory je řízeno z vozíku
Na cestě do centrálního skladu se jeho trasa kříží s koridorem pro kamiony, které přijíždějí nakládat a vykládat uvnitř haly. Na této křižovatce je umístěný řízený přejezd se závorou a semaforem, který kamion zastaví. Zavření závory je řízeno z vozíku, který semafor a závoru aktivuje v dostatečném předstihu, aby mohl bezpečně projet.
Autopilot může zajet mezi dva vysoké stohy a přitom neztratí kontakt
„V centrálním skladu je Autopilot schopný stohovat 4 palety až do výšky 4 m. Stohy palet jsou umístěny vedle sebe a v několika řadách za sebou. Tomuto způsobu stohování říkáme deep lane stacking. Nikde jinde na světě nic podobného neexistuje ani ve Faurecii, ani u jiných zákazníků Toyoty. Unikátnost řešení spočívá v tom, že stacker Autopilot je schopný zajet do volné řady mezi dva vysoké stohy, a přitom neztratit kontakt s navigačním systémem. Stroj to zvládne díky teleskopickému laseru, který se vysune do výšky a přes stohy palet snímá laserový signál odražený od navigačních reflexních pásek (odražečů) umístěných na různých místech ve skladu," popisuje Václav Mareš řešení, jehož klíčovou myšlenku s teleskopickým laserem navrhl a z velké části realizoval Petr Fiala, aplikační technik Toyota Material Handling CZ. Místa uložení v prostoru odvozu i v centrálním skladu jsou předdefinována. Petr Fiala doplňuje koncept, jakým způsobem vzniká objednávka, kolik je stanic, jak celá operace probíhá, jak je automat úkolován:
„Vytvořili jsme dvě zóny pro nakládání, první s jedenácti stanicemi, druhou s dvanácti stanicemi. V každé zóně je dotykový displej od řídicího systému (PLC controller), na kterém si operátor pouhým dotykem vybere stanici, ze které má automat vyzvednout naložené palety a druhým dotykem určí typ přepravovaných KLT boxů. To je vlastně veškerá činnost, kterou musí operátor udělat pro vytvoření objednávky. Díky tomu automat ví, co má provést, co a kam odvézt a uložit v hlavním skladu."
Třetí a poslední displej, kde je nastaven obsah skladu a přiřazeny volné deep lane zóny pro každý druh používaných KLT boxů. V centrální skladu jsou na volné ploše stohovány palety s různými KLT boxy, vždy 4 palety na sobě.
Mezi řídicím systémem a automatem probíhá permanentní komunikace
Petr Fiala pokračuje: „Systém vozíku si po načtení těchto informací sám vybere nejbližší volnou pozici, do které obě palety složí. Vjede do skladu, ověří si, zda je pozice opravdu volná a palety uloží. Pokud by nebyla, vybere si další volnou pozici nebo zastaví, přivolá obsluhu skladu a bude čekat na nějakou interakci. Mezi řídicím systémem a automatem probíhá permanentní komunikace. K vysunutí laseru dochází právě jen v centrálním skladu. Když vozík po načtení lokace vjede do skladu, zpomalí a vysune teleskopický laser do maximální výšky. Díky tomu probíhá nepřetržitá navigace a stroj nezůstane neřízen, doslova nezůstane slepý, ani na zlomek sekundy. I přes stohy palet, i v hloubce vysokého stohu se stále přesně orientuje, ví přesně, kde je a co má dělat. Při výjezdu ven postupuje opačně."
Ostatní technologie vozíku Autopilot ve Faurecii jsou standardní, stejné jako u všech ostatních řešení Autopilot v ČR i v Evropě. V systému vozíku je nahrán kompletní layout skladu, všechny pozice odkud odebírá a kam ukládá náklad. Svoji pozici neustále přepočítává a orientuje se přitom pomocí reflexních pásek (odražečů), které jsou umístěny po celé trase automatu. Ve výšce 2,90 m ve výrobní a logistické hale, 4,20 m v centrálním skladu.
Nasazení automatů chceme rozšířit
„Žijeme v době digitalizace a častějšího zavádění autonomních řešení. Automatizujeme výrobní procesy i interní pohyby ve výrobě, kde budeme pravděpodobně také testovat i nějaká řešení od Toyoty. Co se týče logistiky a manipulace ve skladu, nyní jsme začali s první operací a s prvním automatickým zakladačem Autopilot. Do budoucna bychom chtěli určitě nasazení automatů rozšířit. AGV vozík ale musí zajistit komplexní proces včetně uložení na konci trasy. Použít tažnou soupravu a mít operátora, který obaly vyloží, pro mě nic neřeší, potřebuji zajistit kompletní manipulační proces. První krok je ale dokončení tohoto projektu a nasazení automatu do reálného provozu. Pak se teprve budeme dívat dál," dodává Václav Mareš a pokračuje:
„Jaké byly alternativy? Projekt začal před více než dvěma lety, osloveno bylo více dodavatelů, ale jen Toyota projevila ambici vyhovět požadavku na automatické stohování až do výšky 4 m a dotáhla projekt do konce. Ostatní se náročného technického řešení zalekli."
Pro Faurecii jde celosvětově o nasazení prvního automatického stackeru i o světovou premiéru využití automatické manipulace s teleskopickým stožárem, přestože Toyota jen v Evropě umístila v mnoha provozech již přes 800 AGV vozíků všech typů. Václav Mareš na závěr uvádí:
„Teď, když projekt finišuje, zajímá se o něj mnoho kolegů z managementu, logistiky i technických oddělení celé divize. Vnímají naše písecké řešení automatizace manipulace jako velkou inspiraci pro celou skupinu Faurecia, a zájem o AGV je ve Faurecii obrovský."
Další článek: Webinář jako důležitý nástroj marketingové komunikace