Inovace ve výrobě letadel s obráběcími nástroji ISCAR
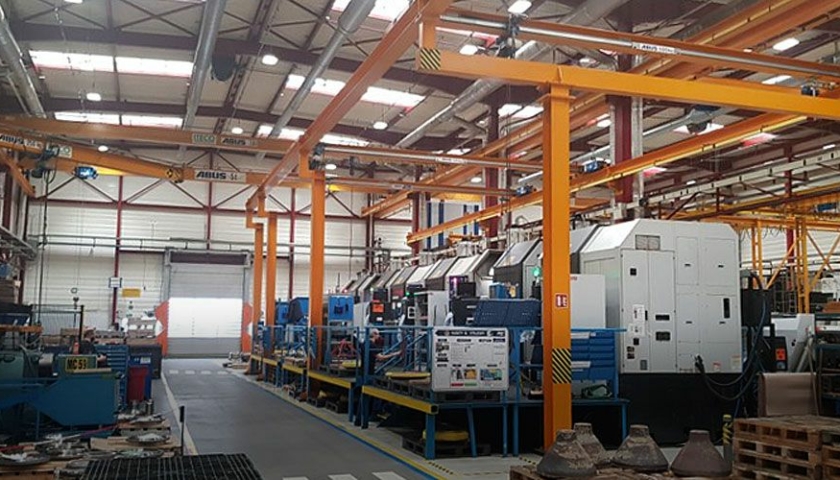
V plzeňské firmě Precision Castparts CZ (PCC) vznikají díly pro výrobu letadel, patřící do skupiny těch kritických. Obrábění ušlechtilých materiálů, hledání nových technologických možností a plnění náročných požadavků je tak v PCC na denním pořádku.
Inzerce
Zaměříme-li se na globální rozsah celé korporace PCC Forged Products, zjistíme, že zde vyráběné díly se nacházejí ve většině letadel. PCC je předním světovým výrobcem komplexních výkovků a mimo odvětví leteckého průmyslu dále nabízí největší škálu výkovků z exotických slitin na bázi niklu a titanu i pro mnohá další odvětví, například těžební či medicínský průmysl. Korporace spravuje šedesát čtyři závodů po celém světě a zaměstnává necelých čtyřicet tisíc zaměstnanců. Díky rozsáhlým investicím je společnost schopna obsáhnout celý výrobní cyklus od vlastního odlitku přes výkovky, obráběcí operace po nedestruktivní kontrolu materiálu apod. Pobočka v Plzni se začala stavět v roce 2000 na zelené louce v lokalitě Borská pole a v současnosti zaujímá 6 000 m2, jež tvoří zázemí pro bezmála 250 zaměstnanců.
Maximální využití současného vybavení
Obrábění v PCC začíná hrubováním výkovku a končí v tolerancích 0,05 mm. Velký odběr materiálu a jeho specifické vlastnosti kladou extrémní požadavky i na dodavatele obráběcích strojů a nástrojů, kterým věnujeme následující řádky. Strojový park společnosti tvoří do padesáti CNC karuselů a soustruhů převážně pro obrábění v průměrech od 100 do 1800 mm, ale zkušenosti zde mají i s průměrem obrobku 2,5 metru. „Ve výrobě máme karusel z produkce TOSHULIN s rozsahem 2 500 mm, na němž jsme obráběli vhodné díly. Ve spolupráci se společností ISCAR se nám při této obráběcí operaci podařilo uskutečnit zajímavou inovaci v rámci břitových destiček pro zapichovací hrubovací aplikaci. Bohužel se aktuálně výroba velkých kusů přesunula do USA, kde se jim v tomto segmentu otevřely nové výrobní kapacity,“ říká vedoucí technologie plzeňské PCC Tomáš Dlabal.
V PCC převažují stroje karuselového typu od českého výrobce TOSHULIN, najdeme zde však i menší stroje, jako karusely a soustruhy značky Doosan, které si zde pochvalují pro jejich odolnost. Japonsko zastupují značky Mori Seiki, Toshiba či Mazak. Víceúčelové obráběcí stroje nabízí svým uživatelům pestrou škálu výrobních možností: „Tyto stroje mají velký zásobník nástrojů, proto se snažíme, aby v budoucnu mohl jeden operátor obsluhovat až tři stroje bez nutnosti dalších zásahů. V blízké době neplánujeme větší investice do strojového vybavení a musíme se snažit vytěžit maximum z toho, co máme k dispozici. V tomto oboru musí člověk myslet neustále v předstihu, proto stále plánujeme. Aktuálně například využití robotické ruky u šesti CNC strojů, jež bude mít na starost automatickou výměnu nástrojů. Vše je vymyšleno, spočítáno a v rámci dokumentace i nachystáno. Rád bych však nový způsob výroby začal na nových strojích a v novém prostředí,“ upřesňuje vedoucí technologie Dlabal.
České obráběcí stroje odvádí skvělou práci
Ve výrobě nás zaujalo četné zastoupení strojů z portfolia TOSHULIN, s nimiž se v českých firmách příliš často nesetkáváme, neboť jejich velká část je určena pro export. V Hulíně mají s výrobou obráběcích strojů bohaté zkušenosti a zákazníkům nabízí špičkové stroje s integracemi různých technologií třískového obrábění. „Jeden CNC stroj SKIQ 16 a tři modely SKIQ 12 od tohoto výrobce u nás máme od počátku, tedy od roku 2000. Jedná se o čtyři repasované stroje, které běží v režimu 24/7. Po dvaceti letech zde nepřetržitě obrábí niklové slitiny – výkovky, což není úplně snadné. Stále skvěle drží a investice do jejich údržby jsou téměř minimální. Z Hulína máme skutečně mnoho strojů, neboť jsme s nimi maximálně spokojeni. Poslední přírůstek je z roku 2017 a jedná se o Basicturn 2000 S2. Jsou to vlastně geniálně jednoduché a velmi dobře čitelné stroje, navíc maximálně precizní a stabilní. V rámci dalších investic se proto určitě budeme zajímat o aktuální nabídku tohoto výrobce. Velmi kvituji i dostupnost náhradních dílů a servis, to vše hraje při výběru důležitou roli. Dnes se v mnoha směrech dělá bohužel řada věcí zbytečně složitě,“ říká s povzdechem Tomáš Dlabal. Řídicí systémy se snaží v PCC sjednotit, což je praktické zejména v případě rotující obsluhy. Nejčastěji jsou zastoupeni dodavatelé Siemens a Fanuc. Výjimku tvoří stroje Mazak s vlastním řídicím systémem Mazatrol.
Ultrazvukové imerzní zkoušení obrobků
V první polovině roku 2019 investovali v Plzni do tří nových pracovišť nedestruktivní kontroly, jež patří ke špičce v oboru. Využíváno je zde poloautomatizované a automatizované bezkontaktní imerzní zkoušení obrobků, při němž je kontrolovaný díl ponořen do nádrže s vodou, která slouží jako přenašeč ultrazvuku. Pro zjištění necelistvostí v materiálu je využívána metoda impuls – doraz. Do ultrazvukové sondy se přivede napětí, které vybudí ultrazvukový impuls, jenž je skrz vodu přenesen do zkoušeného materiálu. V případě, že signál narazí na defekt uvnitř materiálu, odrazí se zpět do sondy, v níž dojde k přeměně ultrazvuku a napětí, a to se díky ultrazvukovému přístroji přemění na viditelný signál. I v této oblasti je plánováno navýšení produktivity a zjednodušení práce obsluhy, která však musí disponovat matematickými schopnostmi, přesností a trpělivostí, neboť výsledek kontroly není viditelný ihned. „V této oblasti se dlouhodobě potýkáme s kvalifikačním problémem. Řada těch, kteří projdou školením, posléze u této práce nevydrží. Je málo dynamická a vyžaduje určité předpoklady uchazeče, který by měl být až puntičkář a nesmí mu vadit dlouhodobé sezení,“ upřesňuje Tomáš Dlabal. V současnosti v PCC využívají osmnáct ultrazvukových přístrojů od předních českých i světových výrobců, jakými jsou například ScanMaster, ATG, GE, Olympus a další a zkušebna PCC Plzeň právem patří k největším zkušebnám svého typu v Evropě.
Úspora díky inovaci standardní břitové destičky
Kvůli specifickým materiálům jsou kladeny náročné požadavky také na nástroje. Některé náhradní díly pro nástroje si v PCC nechávají dokonce tisknout pokrokovou metodou 3D tisku z nástrojové oceli. Od prvopočátku zde však patří ke stabilním dodavatelům nástrojů společnost ISCAR. V její prospěch hovoří, mimo dostačující rozsah a kvalitu portfolia pro mnohé obráběcí operace, i sídlo pobočky téměř na dosah. Lokální umístění však nestačí, nejdůležitější je vždy precizní výsledek. V rámci dlouhodobě dobré spolupráce zde neustále zkouší a vyvíjí nová technologická řešení obrábění, jež otevírají dveře pro vznik inovativních a jedinečných nástrojů. Korporace PCC Forged Products a ISCAR mají společného akcionáře, což vede k jistému zájmu navýšit odběr nástrojů právě od tohoto výrobce. Nicméně vždy musí být nástroj podložen výkonem, bez něhož by se pro jeho využití v PCC nikdy nerozhodli. V poslední době se výrazně zkvalitnila komunikace mezi centrálami, jež umožnila užší spolupráci na vývoji, testování a zavádění nových typů nástrojů. Českému zastoupení firmy ISCAR to v mnoha směrech uvolnilo ruce. „Vývoj postupuje neustále vpřed a je velmi výhodné se na něm podílet společně. Od ISCAR ČR odebíráme standardní břitové destičky a nástroje, avšak máme i mnoho různých speciálních nástrojů určených pro naši výrobu, které jsme vyzkoušeli a po určitých změnách je zařadili do výrobního procesu. Osobně nechci být závislý na jednom dodavateli, neboť každý musí vyvíjet a inovovat stávající nabídku produktů. A nám to může přinést jedině užitek. Hovořím však i o případných výpadcích v dodávkách, jež samozřejmě mohou nastat. Velmi rád přiznávám, že se díky skvělé komunikaci a vysoké odborné kvalifikaci techniků z firmy ISCAR neustále vzájemně učíme a baví nás společně hledat nové možnosti v technologii obrábění. Aktuálně mohu uvést vytvoření nástroje pro naše specifické potřeby, jenž nám ve výrobě ušetřil mnoho času. Hovořím o nástroji a břitové destičce TCMT. Břitová destička má šířku 24 mm a je na našich strojích schopná produktivně hrubovat, a tedy zrychlit stávající výrobní proces. Po optimalizaci řezných podmínek vydrží v řezu 15 minut na břit. Nástroj je konstruován s chlazením VBD, jak z čela, tak i hřbetu. Použitý tlak je do 35 barů. Destička nám zrychlila výrobní proces řádově o 25 %. Tento nástroj již používáme ve standardním procesu a na jeho základě se zrodila myšlenka nástroje nového, který s techniky firmy ISCAR v současné chvíli testujeme. Jedná se o hrubovací nástroj pro čelní zapichování, jenž budeme zkoušet na výkovcích, které mají větší přídavky materiálu. Nástroje testujeme na šrotových výkovcích ze slitin titanu, protože je důležité, aby se nástroj vyzkoušel na výkovku s kůrou, neboť teprve pak zjistíme, zda funguje a jakou má životnost. Tato aplikace má sice pomalejší řezné parametry, ale v odběru materiálu je mnohem efektivnější než při dosavadním využití kruhových destiček,“ upřesňuje Tomáš Dlabal.
Technická řešení pro vyšší produktivitu s firmou ISCAR
V současné době firma ISCAR dodává do PCC v Plzni standardní ISO destičky jak ve formě katalogových položek, tak i speciálních ISO destiček určených na konkrétní materiály. Dalším hojně využívaným sortimentem jsou katalogové zapichovací a upichovací nástroje s VBD. Aleš Dobrý, projektový manažer pro letecký průmysl ze společnosti ISCAR, dodává: „S PCC spolupracujeme denně a s Tomášem Dlabalem vymýšlíme nová technická řešení pro zproduktivnění výroby. Jakmile máme jasně formulované požadavky, posíláme je na centrálu a čekáme na reakci. Nástroj si necháme vyrobit teprve po pečlivém technickém a ekonomickém vyhodnocení. Jakmile nástroj dorazí, začíná náročná doba zkoušení a mnoha výpočtů a pokud se efektivita prokáže, zařadíme ho do běžné výroby. Hovoříme tedy o nástrojích vyrobených na zakázku, což už dnes musí dělat každý větší dodavatel.“
Velice zajímavý je i způsob, jakým se obrábí slitiny niklu keramickými destičkami. Společnost ISCAR nyní aktivně pracuje na vylepšení řezné keramiky. Další plány směřují i k zapichovacím keramickým destičkám, jež bude možné upnout do standardních držáků. V referencích firmy PCC najdeme ty nejnáročnější zákazníky, jako Siemens, GE nebo Safran, přičemž majoritním odběratelem je letecká divize společnosti Rolls-Royce. Pro Tomáše Dlabala a tým jeho kolegů to znamená jediné – neustále pracovat na inovativních postupech, držet vysokou kvalitu vyráběných komponentů a klást vysoké nároky na vlastní tým i dodavatele. Blízká budoucnost patří v PCC rozšiřování výrobních prostor na vedlejší pozemky, které mateřská společnost nedávno přikoupila.
Další článek: Virtuální Formnext Connect 2020 byl velkou událostí