„Pandemie odhalila sílu aditivní výroby,“ říká český průkopník 3D tisku z kovů
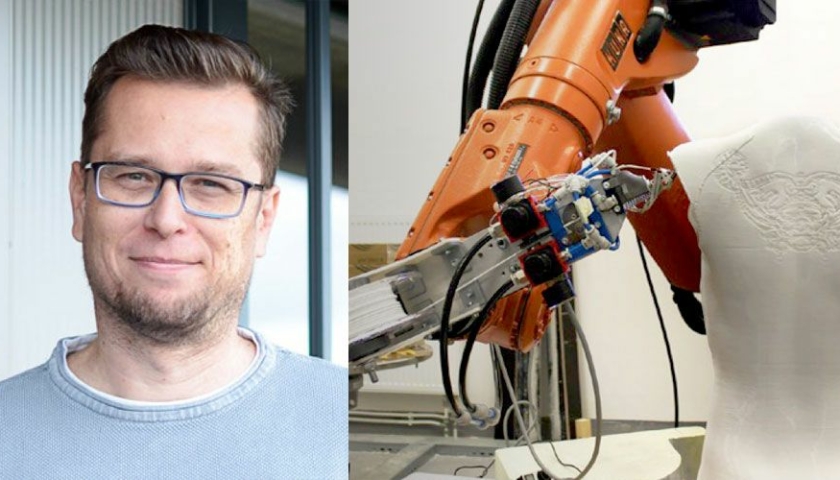
Málokdo má v Česku tak bohaté a vysoce odborné zkušenosti se 3D tiskem z kovových materiálů, jako David Paloušek, který nyní po mnohaletém působení na akademické půdě přesedlal do komerční sféry a v našem rozhovoru se ohlíží za svou dosavadní kariérou.
Od vývoje specializovaných technologií pro aditivní výrobu z práškových kovů přes robotický 3D tisk až po špičkové aplikace pro družice Evropské vesmírné agentury – takové spektrum kompetencí se promítá v následujícím interview prostřednictvím jeho protagonisty. Vzhledem k tomu, že jej s autorem rozhovoru pojí dlouholetá známost, čtenář snad promine, že si zde výjimečně neformálně tykáme.
Patříš k nejzkušenějším profesionálům v oblasti aditivní výroby z kovů u nás. Co a kdy tě ke 3D tisku vlastně přivedlo?
David Paloušek, One3D: Moje cesta k aditivní výrobě byla pozvolná. Na fakultě (FSI VUT v Brně) mě to táhlo k počítačové grafice a 3D modelování. Tehdy, a je to už dvacet let, to byl docela moderní obor spojený se systémovou integrací, síťařinou a programováním. Tamní ústav konstruování už tenkrát disponoval 3D tiskem. V průběhu doktorského studia jsem pak dostal na starosti založit nový studijní obor a podařilo se mi pořídit na tu dobu moderní stroj Stratasys SST 1200 na FDM tisk. Takže k 3D tisku mě vlastně přivedlo vzdělávání.
S jakými technologiemi aditivní výroby jste se na VUT v Brně postupně seznámili a jakým vybavením disponuje tamní pracoviště v současnosti?
Jak jsem zmínil, začínali jsme s FDM tiskem. Fakultě se pak v roce 2012 podařilo získat finance na nové technologie a od začátku roku 2013 jsme zahájili provoz technologie SLM od firmy SLM Solutions pro aditivní výrobu z kovových materiálů. Kromě této technologie jsme pořídili stroj od firmy Z Corporation, který pracuje se sádrokompozitovým práškem (dnes je součástí 3D Systems). Máme k dispozici i všeobecně známou technologii SLA. Ale prakticky se věnujeme v drtivé většině aditivní výrobě z kovů.

Vaše kompetence v aditivní výrobě z kovů značně přesahují aktivity běžného uživatele…

Se svými kolegy ses v rámci akademické práce věnoval řadě působivých vědecko-výzkumných projektů souvisejících se využitím 3D tisku. Mohl bys ty nejvýznamnější připomenout?
Osobně považuji projekty aplikovaného výzkumu za nejzajímavější způsob, jak tyto – u nás nastupující – technologie začít využívat. Jak jsem již zmínil, zajímavým projektem je 3D tisk z hořčíkových slitin. Ve spolupráci s průmyslovým partnerem a kolegy z VŠCHT v Praze zkoušíme najít cestu, jak realizovat díly do lidského těla, které by lidský organismus dokázal vstřebat a nahradit buňkami. Cílem je mj. eliminovat sekundární chirurgické zákroky. Ale musím říct, že je to náročné téma. Úplně jiný příběh jsou projekty pro ESA (Evropská vesmírná agentura). Náš tým realizoval poměrně známý projekt konzoly pro anténu satelitu. Ve spolupráci s brněnským průmyslovým partnerem LK Engineering jsme využili struktur k rapidní eliminaci hmotnosti tohoto komponentu. Prutová struktura je, jak známo, konvenčně nevyrobitelná. V tomto projektu se podařilo dokonce strukturu topologicky optimalizovat. V současné době FSI realizuje projekt s GE Aviation Czech, který je také zaměřen na kosmické a letecké aplikace. V rámci projektu máme možnost realizovat velké díly z výrobně náročných slitin. Tím myslím díly do cca půl metru, což je v aditivní výrobě kovů stále velký díl. V neposední řadě se zabýváme niklovou slitinou pro vysokoteplotní aplikace v kooperaci s leteckým průmyslem. Další oblastí, kterou se zabýváme díky kolegovi Davidu Škaroupkovi, je velkorozměrový robotický 3D tisk. Pracujeme na 3D tisku polymerních betonů, ale také na 3D tisku cementových směsí s několika průmyslovými partnery. Zde vidíme velký potenciál a usilujeme o založení spin-off firmy VUT v Brně. Jsme zapojeni i do velkých výzkumných projektů, například „OP VVV – Materiály s vnitřní architekturou strukturované pro aditivní technologie (ArMadit)“, do Národního centra kompetence Mechatroniky a chytrých technologií pro strojírenství (Mestec) TAČR. Armadit je zaměřen na základní výzkum s potenciálem na konkrétní aplikace, jako je absorpce energie, elektromagnetické aplikace, studená kinetická depozice. Mestec míří částí svého výzkumného programu na konkrétní průmyslové aplikace aditivní výroby v oblasti lidského zdraví, hydrauliky, topologické optimalizace a redukce sestav.
Sleduješ také aktivity ostatních českých univerzit v oblasti aditivní výroby a dokážeš porovnat, jak si v tomto ohledu Česko stojí ve srovnání se zahraničím?
Povědomí mám, ale odpovědět mohu jen obecně. Nechci mluvit za dané kolegy a myslím, že každé pracoviště se snaží vyniknout s něčím originálním a nepřísluší mi to předčasně komentovat. Technologií LPBF (Laser Powder Bed Fusion) disponuje několik vysokých škol, pokud vím tak v Brně, Liberci, Ostravě, Praze, Plzni a v Olomouci. Každé univerzitní pracoviště akcentuje jinou oblast využití aditivní výroby z kovů. Srovnání se zahraničím je ošemetná věc. Je jasně vidět, že v Německu, kde jsou čtyři největší výrobci strojů, jsou v této oblasti několik let před námi. Také Fraunhofer, Laser Centrum Hanover, Airbus, silná ekonomika, silné technické univerzity, to vše umožňuje hnát vývoj rychle dopředu. Ale to není jen případ Německa, vůbec západní Evropa je progresivní v oblasti aditivních technologií nejen v kovech, ale třeba také ve stavebnictví. Co jsem měl možnost vidět v minulých letech na konferencích a porovnat s tím, co se dělá u nás, tak aktivity našich univerzit v této oblasti narostly až někdy v roce 2014. Konečně, lze to dohledat v citačních databázích.
Po čtvrt století na akademické půdě ses nedávno rozhodl přejít do komerční sféry – jaká máš s tímto krokem spojená očekávání?
Velká (říká s velkým úsměvem). Já jsem srdcař a očekávám, že se mi podaří přispět k rozvoji aditivní výroby a k intenzivnějšímu využití aditivních principů v průmyslových aplikacích. Konečně vidíme sami, jak se tyto technologie etablovaly v okolních zemích. Také jsou tu firmy, které mají v ČR již několik strojů a aditivní výrobou produkují finální výrobky. Takže prostor tu je.
V září ses stal technickým ředitelem společnosti One3D. Čím se v ní zabýváte?
Firma One3D, kde teď nově působím, je úžasná parta lidí, která už 5 let dodává na trh profesionální aditivně vyrobené díly a pomáhá firmám implementovat tzv. DfAM (design pro aditivní výrobu) do vývoje. Našimi hlavními produkty jsou plastové díly z technologie SLS (selective laser sintering), SLA (stereolitografie) a MJF (multi jet fusion). Dodáváme převážně pro automobilový, letecký a vojenský průmysl, také do oblasti medicíny, produktového designu apod. Specializujeme se na postprocessing, což je u aditivní výroby zásadní technologický krok a umíme realizovat různé druhy povrchů a textur. Zajímavá je technologie vyhlazování povrchu dílů ve vakuu, kterou máme v ČR pouze my. Díky vyhlazování mají naše díly výrazně hladší povrch, a tedy i lepší únavové a mechanické vlastnosti. Disponujeme třemi SLS stroji, velkorozměrovým SLA a poměrně novou technologií MJF od HP. S mým nástupem firma začíná najíždět na aditivní výrobu kovových dílů. To vyžadovalo také posílení vývojového týmu a zavedení nových postupů kontroly kvality výroby. Mezi naše hlavní zákazníky patří například Hella Autotechnik Nova, Varroc Lightning Systems, Škoda Auto nebo Česká zbrojovka.

Jak bys ohodnotil přístup českého průmyslu k využívání technologií aditivní výroby? Jak moc je již jejich potenciál využíván a kde jsou dosud největší rezervy?
Malou stolní tiskárnu dnes člověk najde skoro v každé vývojové firmě. Nejedná se jen o strojírenství, ale třeba elektrotechnické firmy používají low-cost tiskárny pro prvotní návrh krytů, uchycení elektroniky apod. Pokud se budeme bavit o DDM (Direct Digital Manufacturing) nebo o průmyslovém prototypování, tak řada českých firem využívá aditivní výrobu pravidelně. V oblasti plastových dílů zájem firem roste a konstruktéři a vývojáři se v problematice začínají orientovat. Odhaduji, že v ČR může být minimálně několik desítek průmyslových tiskáren (SLS, SLA, MJF, FDM). Co se týká kovových dílů, možná bychom byli překvapeni, kde všude je SLM technologie vyžíváno a kolik strojů je již v republice v provozu. V porovnání s konvenčními výrobními technologiemi jsou to sice počty úsměvné, ale zohledníme-li cenu, novost, trh, nedůvěru a nízkou edukaci, tak to není zas tak špatné. Služby průmyslového 3D tisku v ČR zastupuje pár firem, je tu také poměrně vydatná konkurence ze zahraničí. Rezervy spatřuji v důvěře v technologie aditivní výroby, jejich návratnost, a také v jejich zavedení do prototypové nebo běžné výroby. Určitě je zde stále nízká informovanost a podpora vzdělávání.
Několik let jsi působil jako prezident oborového sdružení Klastr aditivní výroby, které však nakonec zaniklo. Jaké sis z toho odnesl zkušenosti – znamená to například, že firmy působící v oblasti aditivní výroby v ČR necítí skutečnou potřebu prosazování společných zájmů?
Původní myšlenka mít oborový klastr se mi líbila, ostatně, byl jsi u toho, a proto jsem na nabídku kývl, jako nezávislá osoba z nekomerční sféry. To, co jsem považoval za nejdůležitější, byla edukace v této mladé oblasti. A stále si to myslím. Bez vzdělání a pochopení benefitů, bez pochopení konstrukčních a technologických zásad, bez pochopení nevýhod a limitů nemůže být nová technologie rychle a spolehlivě přijata. Toto mé vidění světa bylo odlišné od problémů, které řešili partneři v klastru. Proto jsem se již dva roky před ukončením fungování klastru rozhodl na funkci rezignovat. Klastr nenaplnil má očekávání v oblasti popularizace aditivní výroby. Paradoxně dnes o to víc slyším, že „evangelizace“ 3D tisku je prostě nutná. A nejen 3D tisku. Je potřeba vzdělávat i v navázaných aplikacích, kontrole kvality, CAD/CAM/CAE softwarových nástrojích, materiálech atd. Otázka byla ale na prosazování společných zájmů. Popravdě nevím. Pokud by tím zájmem mělo být vzdělávání, tak já jsem připraven.
Troufneš si odhadnout – i na základě zkušeností z posledních měsíců – jakým způsobem se projeví koronavirová pandemie na využívání technologií 3D tisku?
Pokud mohu mluvit jen za firmu One3D, tak dopad zatím není významný. Pokud by však situace měla trvat ještě řekněme půl roku, můžeme pocítit ztráty v některých segmentech našeho cílového trhu. Ale! Osobně, a to vůbec nechci zlehčovat lidské životy a těžké osudy mnoha, kterých se krize dotkla, vidím tuto situaci i jako příležitost pro nové technologie a přístupy. Z první vlny vidíme, jak se začaly aditivní technologie používat na všech úrovních, od „hobíků“ po firmy, jak rychle mohly být ochranné pomůcky vyvíjeny a vyráběny. To byla krásná ukázka, jak aditivní výrobu využít. Spousta lidí si uvědomila, co všechno mohou 3D tiskem dělat. Nedokážu vyčíslit, jak moc koronavirová krize ovlivní nasazení aditivní výroby. Oblast totiž celkově neustále roste a tuto analýzu si snad přečteme v ročence Wohler’s Report za jeden či dva roky. Rozhodně dopad do tohoto segmentu bude kopírovat okolní situaci, podobně jako v roce 2009. Držme si palce a pozitivní myšlení.
Článek vyšel v časopisu STROJIRENSTVI.CZ
Další článek: Jak fungují různé typy pohonů – ve srozumitelných animacích