Strategie pokročilého hrubování – rychlost díky optimální dráze nástroje
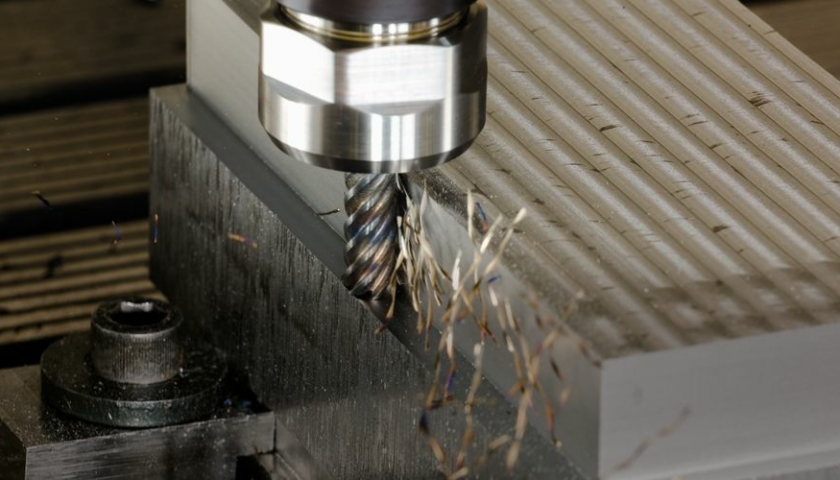
Optimalizace drah nástroje s použitím CAM systému je využívána již celkem dlouho. V posledních deseti letech však začali v Seco Tools kombinovat tyto možnosti s novými strategiemi obrábění a speciálně konstruovanými frézami.
Takové strategie obrábění, které šetří čas a náklady, označujeme jako dynamické frézování či pokročilé hrubování. Možnosti CAM softwaru se využívají pro účely kontroly záběrového úhlu nástroje a střední tloušťky třísky. Přizpůsobování úhlu opásání nástroje pomocí dráhy generované CAM systémem umožňuje zvýšení rychlosti hrubování, efektivní kontrolu teploty v procesu a použití vyšších hodnot posuvu na zub a hloubky řezu, což zásadně zkracuje cyklový čas výroby součástí – to vše bez zvýšeného namáhání vřetena stroje.
Záběrový úhel a tepelné zatížení
Úhel záběru nástroje je nezávislou proměnnou, která ovlivňuje tepelné zatížení nástroje a je klíčem k optimalizaci hrubovacích operací. Maximální úhel záběru jakékoliv frézy je 180 stupňů – celý průměr v řezu. Při plném úhlu opásání je tedy radiální hloubka řezu stejná jako průměr nástroje. Změnou úhlu lze snížit množství tepla, které v průběhu hrubovací operace vzniká. Zmenšuje se radiální hloubka řezu, a tedy i záběrový úhel. Menší délka oblouku kontaktu zkracuje čas v řezu, a proto vznikne mezi břitem nástroje a stěnou obrobku méně tepla. Současně má břit v rámci každé otáčky nástroje, kdy je mimo řez, delší čas na ochlazení. Nižší teploty při obrábění umožňují zvýšit řeznou rychlost a zkrátit cyklový čas.

Střední tloušťka třísky a mechanické zatížení
Střední tloušťka třísky vychází z mechanického zatížení a ovlivňuje ji kombinace posuvu na zub a záběrového úhlu. Protože se tloušťka třísky při frézování neustále mění, pracujeme s její průměrnou hodnotou a nazýváme ji střední tloušťkou třísky (hm). Při plném úhlu záběru (180°) vznikají třísky o největší tloušťce ve středu šířky nástroje. Je-li úhel záběru menší než 90°, dochází ke snížení tloušťky třísky, a pro její zachování je třeba zvýšit posuv na zub (fz). V prvních 90° záběru se jedná o nesousledné frézování – až po dosažení maximální tloušťky třísky – a ve zbývajících 90° pak jde o frézování sousledné, kdy se tloušťka třísky opět snižuje až k nule. Pokud se ae sníží (ae < 0,5×DC), například na 1 mm (10 %), snižuje se i hodnota střední tloušťky třísky – a to umožní zvýšení posuvu na zub (fz) a zrychlení operace. Břity nástroje odebírají menší objem materiálu, ovšem v mnohem rychlejším taktu. Současně dochází ve srovnání s obráběním při větších radiálních hloubkách záběru a nižších hodnotách posuvu k menšímu namáhání nástroje i vřetena stroje. Při hrubovacích operacích dynamického frézování umožňuje malá radiální hloubka řezu (AEMX) zvětšit axiální hloubku řezu (APMX) a úběr materiálu ještě zvýšit.

Konstrukce nástroje pro pokročilé hrubování
Základním typem nástroje pro tuto strategii je monolitní karbidová fréza. Většina výrobců obráběcích nástrojů nabízí produkty podle zaměření na různé materiály. Někteří z nich, včetně Seco Tools, však vyvíjejí též geometrie pro pokročilé metody obrábění. V případě hrubovacích strategií založených na využití CAM softwaru je klíčovou záležitostí utváření třísky, dostatečná délka břitů a prostor v drážkách frézy.
Pro pokrytí nejširšího spektra obráběných materiálů je v rámci sortimentu Seco k dispozici pro operace pokročilého hrubování řada fréz JS560, specializovaná pro dynamické frézování. Konstrukce těchto nástrojů zajišťuje zvýšenou stabilitu a nižší průhyb, což zvyšuje bezpečnost obráběcí operace. Pro obrábění hlubokých kapes a 3D tvarů metodou dynamického frézování (pokročilého hrubování) jsou běžné délky břitů troj- až čtyřnásobkem průměru frézy. Aby bylo možné tyto operace provádět i v náročných materiálech, jako jsou například nerezové oceli či titan, připravilo vývojové oddělení Seco řadu vícebřitých fréz JS720. Tyto nástroje umožňují naplno využít potenciál obráběcího stroje i CAM programování a zajistit maximální spolehlivost procesu pokročilého hrubování.
Konstrukce a možnosti nástrojů
Je-li během obrábění udržován konstantní úhel opásání, jsou projevy opotřebení na břitech nástroje pravidelnější. Výsledkem je pak lépe předvídatelná životnost frézy. Dlouhé břity však způsobují vznik dlouhých třísek, jež není snadné z místa řezu spolehlivě odvádět. Aby vznikaly třísky kratší, které je snazší odvádět, jsou břity fréz Seco geometrií JS564 pro běžné materiály i JS720 pro obrábění materiálů ISO-M a -S vybaveny děliči třísek. Jedná se o záměrné přerušení ostří malými drážkami na obvodu. Navzájem jsou vzdálené o 1×DC (průměr nástroje). U frézy o průměru 10 mm s délkou břitů 40 mm tak vznikají třísky ne delší než 10 mm, které lze ze zóny řezu snadno odstranit a současně prakticky eliminovat i riziko zahlcení dopravníku třísek ve stroji.

Základní pravidla dynamického frézování
Záběrový úhel a počet zubů nástroje – Pokud využíváme malý záběrový úhel, je dobré nasadit nástroj s co největším počtem zubů, neboť vysoká rychlost posuvu zvýší produktivitu (rychlost posuvu = počet zubů × posuv na zub × počet otáček vřetena). Zatímco běžné hrubovací frézy mají nejvýše 4 zuby, sortiment Seco zahrnuje nástroje se 4, 5, ale i více zuby. V případě dobře řízeného procesu frézování s malou radiální hloubkou řezu přinášejí vícezubé frézy obrovský nárůst efektivity. Komplexní tvary obrobků – Při obrábění po přímé dráze (boční frézování) zůstává nastavený záběrový úhel konstantní. V případě obrobků komplexních tvarů, které zahrnují vnitřní a vnější rádiusy, je ale záběrový úhel nepravidelný. Když fréza dokončí přímý řez a vstoupí do vnitřního rádiusu či koutu, záběrový úhel se skokově zvýší – a to znamená, že řezné parametry nastavené pro původní konfiguraci již neplatí. Pokud na tuto skutečnost řídicí systém nezareaguje, dojde k rozechvění a vibracím, nebo dokonce zničení nástroje.
Dráhy nástroje a jeho průměr ve vztahu k rozměrům obrobku – Současné CAM systémy nabízejí i strategie pohybů nástroje přizpůsobené tvarům s vnitřními a vnějšími rádiusy, kde se proměnlivé úhly záběru kombinují s běžnými přímými drahami. Tyto softwarové balíčky automaticky upravují rychlost posuvu podle aktuálního úhlu záběru a udržují tak stejnou tloušťku třísky. Pro zachování konstantního úhlu záběru i v oblastech rádiusů využívá software techniky trochoidního frézování a metody Peeling. Dokáže se tak vyhnout ostrým tvarovým přechodům a ještě více zkrátit cyklový čas.Při využití optimalizovaných drah pro hrubování a udržení konstantního úhlu záběru může být průměr nástroje dokonce stejný, jako je vnitřní rádius na obrobku, a přesto nedochází k přetížení nástroje či nabírání a zařezávání materiálu. Navíc umožňuje odebírat i větší přídavky při hrubování a ponechávat o to menší a pravidelnější pro dokončování – to vše znamená zkrácení času obrábění.
Materiál obrobku – Optimalizované strategie hrubování lze aplikovat u různých obrobků ze specifických materiálů. Nástroje Seco jsou připraveny pro obrábění oceli, nerezi, litiny, titanu, hliníku i kalených ocelí do 48 HRc. Výchozí doporučení bývá pro běžné materiály (P1, 2, 3, 4, M2, K2) typicky 10–15 % AEMX vůči průměru nástroje. Pro obtížně obrobitelné materiály (S2, S12, M4, P12, H7) je doporučeno pracovat s 5 % AEMX a optimalizované rychlosti a posuvy pro tyto záběrové úhly lze získat v aplikaci Seco Suggest na webové stránce www.secotools.com. Je samozřejmě možné využít i větších šířek řezu ae, než je doporučeno, ale pak je nutné počítat se zásadním snížením řezné rychlosti i posuvu na zub.
Obráběcí stroj – U lehčích strojů, které nejsou schopné zvládat těžké hrubovací obrábění, lze jednoduše snížit úhel záběru a využít trochoidní dráhu nástroje. To sníží řezné síly a potřebu výkonu na vřetenu stroje, a přitom stále udržuje vysokou produktivitu, protože se pracuje s velkou axiální hloubkou řezu. Takto se lze vyhnout vysokým potenciálním investičním nákladům a produktivní hrubovací obrábění provádět i se stávajícím strojovým parkem.
Chlazení – Jsou-li metody pokročilého hrubování aplikovány na obtížně obrobitelné materiály, jako například nerezové oceli či titan, je třeba použít účinné chlazení po celé činné délce nástroje – břity je třeba chladit na čele, bocích i výběhu drážek. Při obrábění oceli a litiny je doporučeno použití stlačeného vzduchu, který zaručí ten nejúčinnější odvod třísek.
Řídicí systém a CAM – Pokročilé programy pro dynamické frézování je třeba připravovat mimo systém stroje. Dodavatelé CAM systémů nabízejí různé doplňkové a přídavné moduly, které slouží pro optimalizaci drah nástrojů. Zadávat hodnoty záběrového úhlu doporučené výrobcem nástroje přímo přes řídicí systém stroje samozřejmě lze, ale pouze v případech jednoduchého hrubování po přímých drahách, případně ve fixních trochoidních cyklech.
Průvodce dynamickým frézováním
Jak maximalizovat úběr materiálu při minimálním opotřebení nástroje? Dynamické frézování (známé také jako optimalizované nebo pokročilé hrubování) je odpovědí pro ty, kteří chtějí ve srovnání s tradičními frézovacími strategiemi zlepšit efektivitu hrubovacích operací při zachování vysoké bezpečnosti procesu a dlouhé životnosti nástroje. Stáhněte si zdarma e-book „Průvodce dynamickým frézováním“ na webu www.secotools.com/article/119125.
Záběrový úhel nástroje a střední tloušťka třísky jsou klíčem pro optimalizované hrubovací strategie. Pomocí CAM softwaru specializovaného pro optimalizaci drah nástroje a metody dynamického frézování lze řídit úhel opásání a udržovat konstantní zatížení břitů. Tak je také možné kontrolovat teplotu během procesu a využívat vyšší řezné rychlosti a posuv na zub v kombinaci s velkou axiální hloubkou řezu pro významné snížení cyklového času obrábění. Je však třeba mít na paměti, že pokročilé hrubování vyžaduje vhodný CAM software pro externí programování. Dále také skutečnost, že většina výrobců přizpůsobuje nástroje materiálům obrobků, a jen někteří vyvíjejí nástrojové geometrie pro různé pokročilé strategie a dráhy obrábění. Se správným nástrojem a dynamickým cyklem lze ve srovnání s konvenčními metodami obrábění zásadně zvyšovat úběry materiálu.
Další článek: Toyota vidí budoucnost automobilismu ve vodíku