Zvýšený objem výroby řeší Bosch Diesel nasazením automatických tahačů
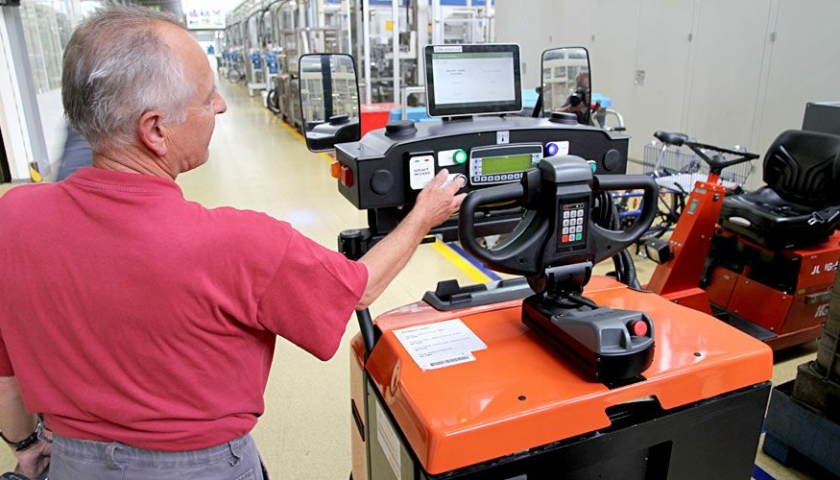
Ve výrobním závodě Bosch v Pávově by bylo další navýšení pohybu manipulačních vozíků s nákladem již neúnosné. Přesto bylo potřeba dosáhnout vyššího toku materiálu. Řešení nabídly autonomní tahače Toyota.
Inzerce
Bosch Diesel v Jihlavě zaměstnává ve třech závodech přes 4 700 lidí a je největším zaměstnavatelem na Vysočině. Výrobu zahájil v roce 1993 a postupně se stal také producentem číslo jedna ve vstřikovacích systémech Common Rail v rámci celé skupiny Bosch. Objem výroby navíc neustále roste, což přináší nové výzvy v logistice a ostatních obslužných provozech. Nové požadavky vyústily v realizaci moderního řešení, které dodala Toyota.
Více materiálu, méně pracovníků
„Byli jsme nuceni reagovat na rostoucí požadavky na převozy ze skladů i v rámci výroby. Nechtěli jsme ale rozšiřovat již tak značný počet souprav, počet jízd a počet obslužného personálu a uvažovali jsme tedy i o nějaké formě automatizace. Chtěli jsme najít řešení s rozumnou dobou návratnosti, zůstat personálně neutrální nebo dosáhnout dokonce určité snížení počtu pracovníků," vysvětluje Pavel Jelínek, vedoucí projektového týmu logistiky.
Jak vypadá výsledné řešení?
Automatický tahač zajišťuje materiálový tok obalů a svoz hotových výrobků na nejdelší trase o délce přibližně 1 km. 900 metrů jede stroj v automatickém režimu. Jeden pracovník soupravu naloží a pomocí ovládacího tabletu, který je na soupravě umístěn, ji odešle. Na místě určení její řízení převezme pracovník, který v krátkém úseku necelých 100 metrů na 8 stanovištích provede postupně vykládku materiálu a obalů a nakládku hotových výrobků. „Na tak krátkých úsecích nemělo smysl řešit automatický pojezd, který stejně vyžaduje povel obsluhy k přejezdu na další zastávku. V tomto úseku bylo zachování manuálního provozu nejefektivnější. Po vyřízení nakládky na poslední zastávce je souprava odeslána zpět do skladu na výchozí stanoviště,“ shrnuje Pavel Jelínek a pokračuje:
„Na digitalizaci na různých úrovních pracujeme již několik let. Naše aktivita v oblasti fyzické logistiky je taková, že se snažíme eliminovat mechanické procesní kroky využitím mobilních technologií. Všechny naše skladové procesy jsou buď realizovány nebo potvrzovány mobilními zařízeními (např. RFID technologií). Jedním z velkých bloků, který jsme museli řešit, je i zásobování výroby, kde jsme hledali potenciál pro zlepšení efektivity a zvýšení bezpečnosti."
Realizaci předcházelo dlouhé hledání
Pavel Jelínek konstatuje, že je velký rozdíl implementovat automatizaci do nově vznikajícího provozu nebo do již stávající a plně funkční zavedené výroby, která je svázaná velkým množstvím restrikcí. „Šli jsme do věci, o které jsme měli jen základní informace, jak funguje. Neuměli jsme dohlédnout na všechna úskalí projektu. Konzultovali jsme interně i externě v rámci jiných divizí skupiny Bosch, ale nikde neměli s automatickou manipulací zkušenosti. Poptali jsme více dodavatelů. Zajímalo nás, jaké technologie a jaké know-how bylo ve své době k dispozici, zajímali jsme se i o zkušenosti z praxe. Konzultovali jsme s více firmami, které se zabývají autonomními technologiemi, nejen s dodavateli manipulační techniky."
"Studie proveditelnosti autonomního řešení jsme provedli již v roce v 2015 a poté se naplno pustili do přípravné fáze. Posuzovali jsme všech původních 7 milk-runů (12 m dlouhé soupravy s řidičem), které se starají o zavážení materiálů do výroby a prověřili jejich vhodnost z hlediska tras, frekvence zavážení materiálů a odvážení hotových výrobků, používaných nosičů nákladů a jejich složení (palety, KLT boxy, skejty). Alternativní řešení, například tahač řízený magnetickou páskou, se neosvědčilo. Rychlost neodpovídala potřebám intenzivní manipulace. Velký počet jízd se podepsal i na častém poškození pásky. Ukázalo se také, že vzhledem ke struktuře materiálového toku nebude možné přejít na stoprocentní automatizaci. Jde tedy o kombinaci manuálního a autonomního provozu. V rámci nového designu transportního konceptu jsme se rozhodli nahradit automatem jeden z milk-runů, ten nejdelší,“ říká Pavel Jelínek.
Bezpečnost je jištěna do detailu
Celá trasa je rozdělena do clustrů, které umožňují nastavení předností a bezpečnostních parametrů, tak, aby se vozíky bezpečně minuly nebo vyhnuly. Okolí si musí zvyknout, sžít se s nehlučně se pohybujícím strojem. V největší hale je také největší koncentrace ostatních milk-runů i pracovníků. Na trase jsou šatny, kde při výměně směn prochází stovky lidí.
Pavel Jelínek vypočítává, co všechno Bosch udělal pro maximální bezpečnost: „Automat má přednost na křižovatkách, kde se může potkat s jinými manuálně řízenými vozíky. Pokud by se měl potkat před zatáčkou nebo před křižovatkou s jiným automatem, díky napojení na řídící software (přes wi-fi) ví, který z vozíků má přednost. Souprava je v kontaktu se stovkami lidí, po trase se pohybují chodci i cyklisté. Je uklidňující, že je automat vždy na vyšší úrovni než manuálně ovládaný vozík. Bezpečnost jsme si pohlídali tak, abychom eliminovali i velmi nepravděpodobná rizika. Se soupravami nelze couvat a například prostor mezi soupravami jsme zajistili ochrannými pásy, aby mezi ně nemohl z nepozornosti vstoupit chodec."
Jak vozík sledují a jak vyhodnocují provoz
Vozík je naprosto spolehlivý a jeho provoz není průběžně nijak monitorován. „Nicméně máme software, kde můžeme sledovat polohu vozíku, zdali měl během nějakého časového úseku nějaké problémy, neplánované zastávky a podobně. Umí poslat chybové zprávy v případě neplánované zastávky, když narazí například na pevnou překážku, kterou někdo nechal na trase. Systém pracuje autonomně, bez naší součinnosti," upřesňuje Pavel Jelínek.
Průkopníkem v rámci skupiny, spolupráce pokračuje
Úspěšný Autopilot se stává modelovým řešením v rámci skupiny Bosch i pro další regiony v Evropě. Pavel Jelínek potvrzuje, že je jisté rozšíření do dalších hal v Jihlavě, protože projekt se maximálně osvědčil a potvrdil všechna očekávání: „Automatizaci budeme určitě dále rozvíjet, ale tak, aby to bylo efektivní a byla tam rozumná návratnost. Automat není možné využít všude. Kooperace s Toyotou v automatizaci pokračuje v dalších projektech, například na automatické ručně vedené zakladače. Systém již máme a je dál využitelný. Software platíme jen jednou, takže příště už budou náklady na implementaci o dost nižší. Uspořili jsme personální náklady v rozsahu asi 1 člověka na směnu. Lidé se o práci ale bát nemusí. Máme obrovský problém nabrat jakoukoli kvalifikovanou sílu do skladu. Nová místa a nové činnosti pak vznikají v oblasti řízení, v projektové činnosti, v programování.“